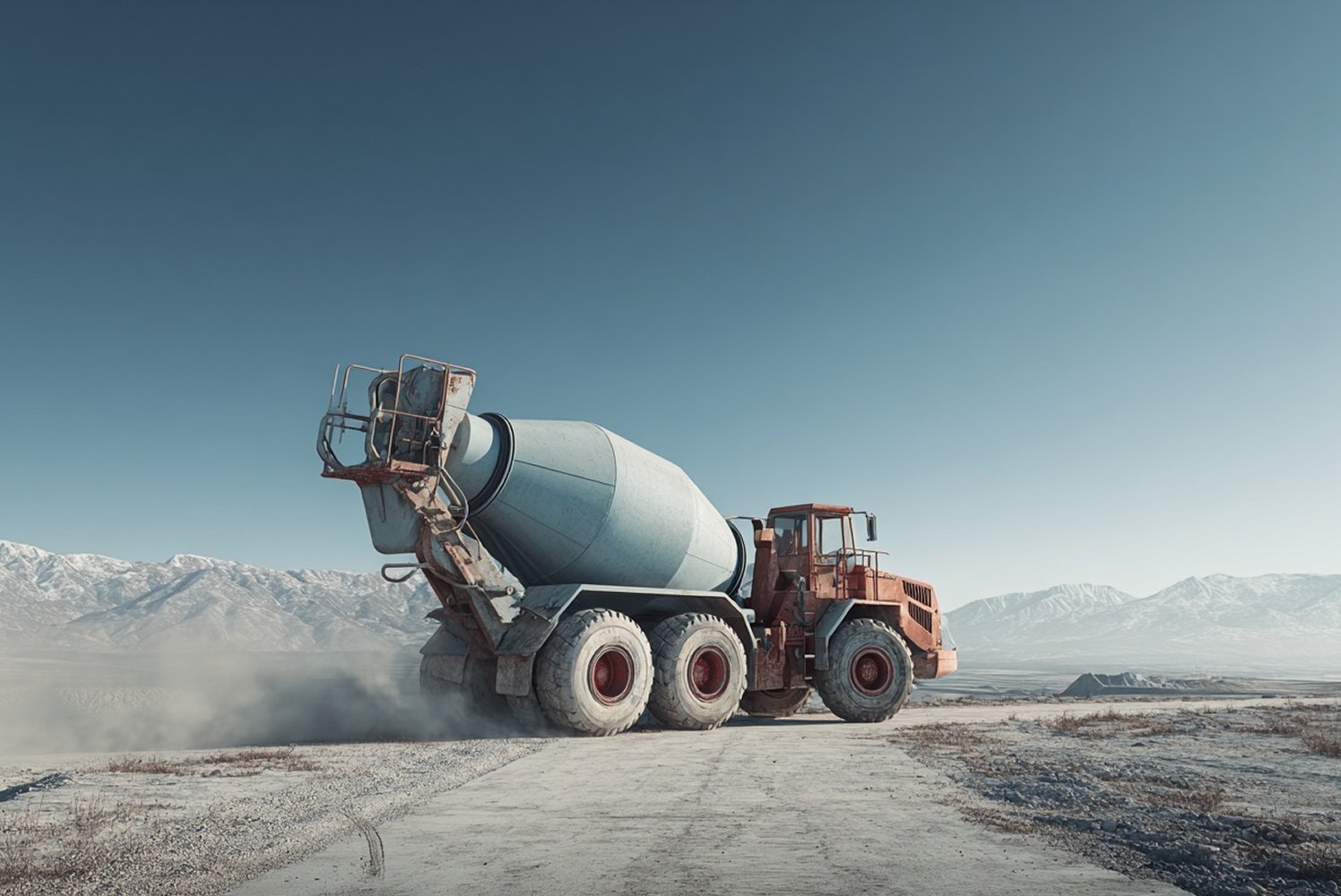
Concrete Dispatch Implementation, That Painful Memory Will Be… Well, Just a Memory
Concrete Dispatch Implementation, that painful memory will be… well, just a memory
Among the most important features of a modern concrete dispatch management system are accessibility, integration, and simplicity. In many legacy systems, these capabilities are lacking. Most legacy concrete dispatch systems were developed over twenty-five years ago, long before smartphones and before wi-fi and Internet access began to become commonplace. With such outdated systems, a seamless connection with mobile technology is not possible, let alone with other standalone systems.
Traditional concrete dispatch systems were built on office hard drives as standalone entities, as was the common practice at the time. It was never intended that they would communicate with other systems or provide mobile accessibility. Due to their isolated nature, they make it difficult to share the latest data among teams and departments, let alone customers.
It is possible to install additional add-ons to help some systems pair up, but the data-transfer process is often complicated and results in redundant information residing on multiple systems. In the event of duplicate data, employees need to figure out which database has the most updated and accurate information, wasting time and resources.
The value of an advanced concrete dispatch system such as ConcreteGO that was designed with integration in mind, rather than as an afterthought, is it can easily connect with other systems such as Batch Control, accounting, inventory management, GPS/truck tracking, and quality control to give concrete dispatchers real-time access to production, delivery and customer data. Ultimately, this results in more efficient operations and greater profitability – Data is no longer a hassle.
Since ConcreteGO doesn’t require multiple server installations and a VPN, it is easy to implement and go live quickly. ConcreteGO can be implemented in as little as two weeks with a dedicated project manager on the customer side.
Learn more about ConcreteGO Cloud Dispatch