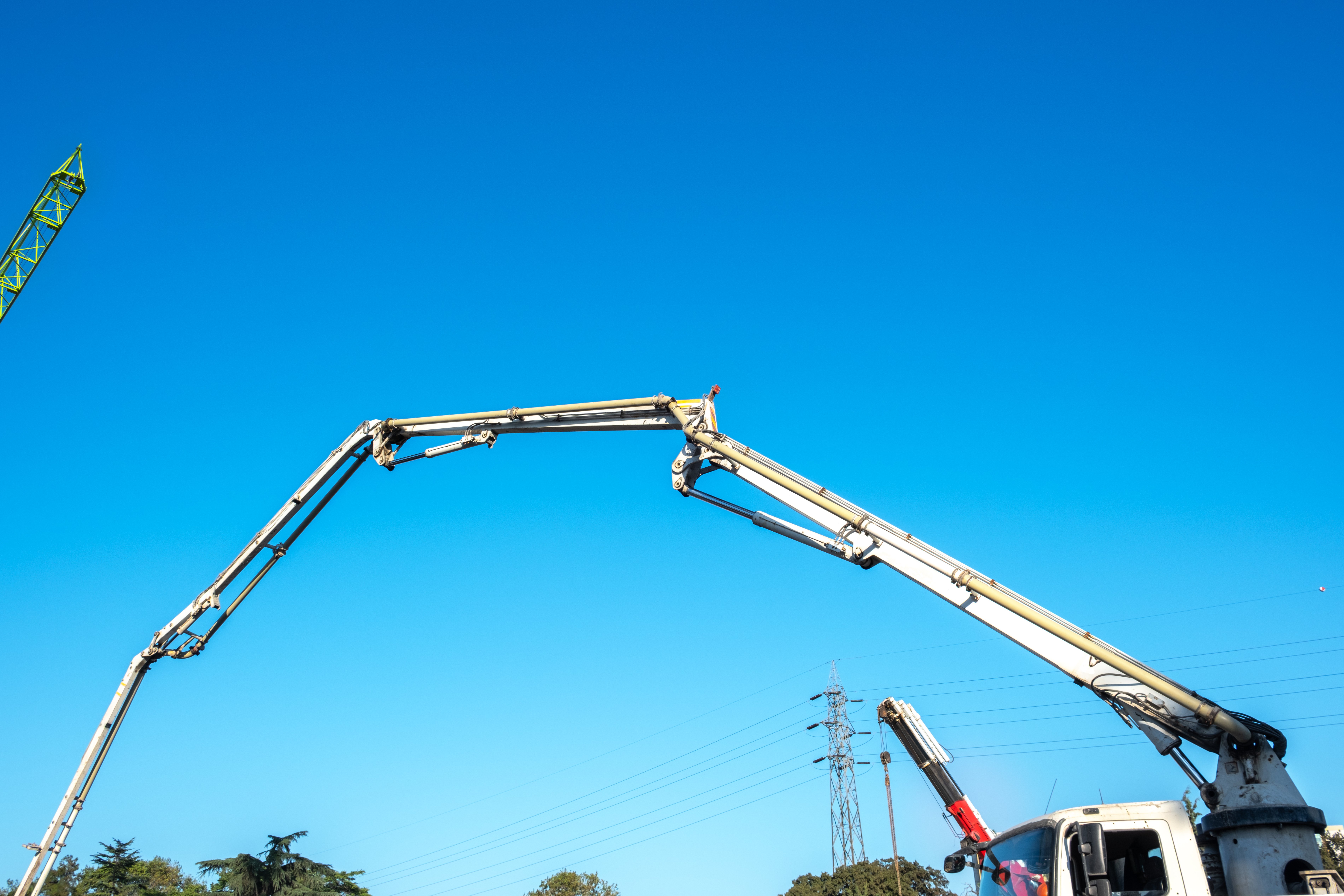
Concrete Pump Truck Productivity KPIs
KPIs That Demonstrate Concrete Pump Productivity
Concrete pump trucks are among the most critical and expensive assets in ready-mix operations. As delivery windows tighten, on-site coordination needs rise, and hourly operating costs grow, efficiency becomes more essential than ever. Ready-mix concrete plant managers can shorten delivery timelines and increase margins by measuring, monitoring, and improving concrete pump truck productivity.
Recent data from MIT shows that the average ready-mix concrete truck delivery time is 120 minutes. If the pump truck is not set up or sequenced correctly, even the most efficient delivery schedule will fall apart. Likewise, delays at the plant or miscommunication with the jobsite can leave a truck sitting idle, burning both fuel and labor costs. With fuel costs on the rise and average delivery costs topping over $144 per hour, waste adds up fast.
Improving productivity is a realistic goal that you can achieve with well-defined operational best practices supported by a modern digital platform, but you need to take one more step.
To move from reactive troubleshooting to proactive improvement, teams need measurable KPIs. Key performance indicators help quantify where productivity is lost, where gains are working, and how to align operations around meaningful results. Metrics such as idle time, time to pour, and cubic yards placed per hour provide objective feedback that helps prioritize both operational and digital improvements.
We’re here to help with proven strategies to increase the productivity of ready-mix concrete trucks and the ready-mix concrete KPIs you need to measure to determine their effectiveness.
Understanding Concrete Pump Productivity Lags
Despite digitization, concrete pump truck productivity has not kept pace with expectations. Not only has truck delivery efficiency plateaued, it’s fallen over the past two decades. Average cubic yards per truck have dropped from to 5,380 in 2023 down from 5,846 in 2005.
Why? Because productivity suffers from recurring bottlenecks such as:
- Lack of coordination between dispatch and field crews
- Poor sequencing between mixer arrivals and pump setup
- Inconsistent use of scheduling and performance tracking
- Limited visibility into jobsite conditions during dispatch
Productivity gains depend on aligning people, processes, and technology, particularly where high value equipment like pump trucks is involved.
Operational Strategies to Improve Challenges to Pump Truck Efficiency
Pump trucks are essential to efficient concrete placement, but too often they are delayed by issues that could be resolved with better coordination and tools. These inefficiencies can cause delays at the jobsite, inflate labor costs, disrupt pour schedules, and limit concrete pump truck productivity. The good news is you can overcome these common challenges by implementing our best practices.
1. Optimize Scheduling for Pump and Mixer Synchronization
When pump and mixer schedules are managed by different foremen or dispatchers, it causes misalignment at the jobsite. Daily coordination calls between plant dispatch and field supervisors confirm timing and adjust for site readiness. This simple step helps prevent idle time, overpours, and unnecessary repositioning.
Related KPIs: Measure arrival-to-pour start time and percentage of on-time truck pairing to evaluate synchronization effectiveness.
2. Reduce Setup and Washout Delays
Unprepared or undertrained crews cannot handle specific pump truck models or boom lengths. Overcome this challenge by using laminated step-by-step setup guides on-site to standardize routines. Assign experienced crews to pump setups and create a buddy program to increase the skills of newer employees.
Related KPIs: Measure time from site arrival to pump positioning and number of repositions required per job.
3. Boost Communication and Task Sequencing
If labor crews aren’t clear on who is responsible for what during setup, priming, or cleanout, it leads to confusion and delay. To overcome this challenge, assign a single crew lead to oversee the entire pump truck process. Conduct a quick task huddle before every pour for better communication among staff members.
Related KPIs: Monitor number of setup-related delays per month and average task duration deviation against plan.
4. Minimize Last-Minute Job Changes
Costly delays often result when field crews make unannounced adjustments to pour zones, requiring the pump truck to reposition mid-pour. You can keep this from occurring by expecting that all changes to be communicated and approved during the pre-pour coordination meeting and requiring pump operators to be present.
Related KPIs: Track frequency of mid-pour repositioning and minutes of delay per reposition
Digitize Operations to Increase Concrete Pump Truck Productivity
The latest technology in ready-mix concrete improves concrete pump truck productivity. Today’s platforms eliminate communication gaps, reduce manual errors, and give teams better visibility into daily operations. These technologies enhance your well-run processes and established best practices, allowing teams to work faster and more consistently with fewer disruptions.
These strategies employ digital systems to help maximize uptime and reduce wasted motion from dispatch to delivery to pour tracking:
1. Integrate Pump and Mixer Dispatch for Better Sequencing
In older dispatch systems, pump trucks are often managed separately from mixer trucks, creating gaps in scheduling and coordination. Modern platforms enable teams to manage pump and mixer dispatch together, ensuring better sequencing and fewer delays at the job site. This improved technology also provides visibility into delivery status, material flow, and crew activity to keep plant and field teams aligned from the start of the pour to the finish.
Related KPIs: Measure dispatch alignment accuracy and on-site idle time per truck. Track on-time delivery rates and cycle time per load
2. Leverage Telematics to Monitor Performance in Real Time
Outfitting pump trucks with telematics provides data on location, setup duration, idle time, and fuel use. This visibility allows supervisors and dispatchers to spot delays as they happen and adjust on the fly. Over time, the data also supports better planning by revealing which sites, crews, or routes are experiencing lower productivity so that future schedules can be optimized.
Related KPIs: Monitor idle time per site, fuel consumption per hour of operation, and yards per driver hour.
3. Replace Paper Tickets with Digital Pour Details
Missing information, delays handoff, and even handwriting errors on paper tickets lead to poor concrete pour truck productivity. Transitioning to electronic ticketing gives dispatchers, drivers, and jobsite leads real-time access to the same pour specs, mix IDs, and boom requirements. This eliminates the need for back-and-forth phone calls and ensures that pump operators arrive with everything they need to get started without delay.
Related KPIs: Track pour start delays and incorrect ticket numbers.
4. Enable Clear Communication with Mobile Field Apps
Radio calls and one-off text messages create silos and make it hard to keep everyone on the same page during a pour. Mobile apps designed for dispatch drivers and jobsite crews allow for structured communication in real time such as confirming arrival, reporting a delay, or submitting a photo of the setup zone. This reduces confusion during time-sensitive pours and keeps the entire crew looped in from batch plant to pump hose.
Related KPIs: Track average response time for jobsite communication tasks and number of escalated coordination issues.
Use Data to Spot Bottlenecks and Reinforce Gains
Over time, even well-run operations can drift into inefficient patterns that go unnoticed. Operations managers to spot recurring bottlenecks with technology platforms that consolidate historical data on setup times, yards placed per hour, and total idle time. These dashboards give producers a feedback loop to refine processes, hold teams accountable, and measure whether recent changes have actually improved concrete pump truck productivity.
Related KPIs: Today’s best platforms allow customization so that you can monitor and measure KPIs that matter most to your business. That could be any of the KPIs discussed above along with:
- Average fuel consumption per truck
- Setup time versus productive pump time
- Yards placed per hour
- Downtime between pours
- Time from arrival to pour start
Putting Concrete Pump Truck Productivity KPIs into Practice
Improving concrete pump truck productivity doesn't have to add complexity. Begin by removing friction from existing processes. Sysdyne’s quick-to-implement, easy-to-use platform helps ready-mix producers gain full visibility into scheduling, delivery, and jobsite coordination, bringing mixer and pump operations onto a single, integrated system. With flexible features like real-time dispatch, electronic ticketing, telematics integration, and mobile tools for field crews, Sysdyne empowers your team to reduce delays, streamline communication, and make data-driven decisions that improve ready-mix concrete KPIs from end to end.
When every minute and every yard matters, the right platform makes all the difference. Ready to see how Sysdyne can help you increase productivity and boost KPIs on every pour? Request a demo today.