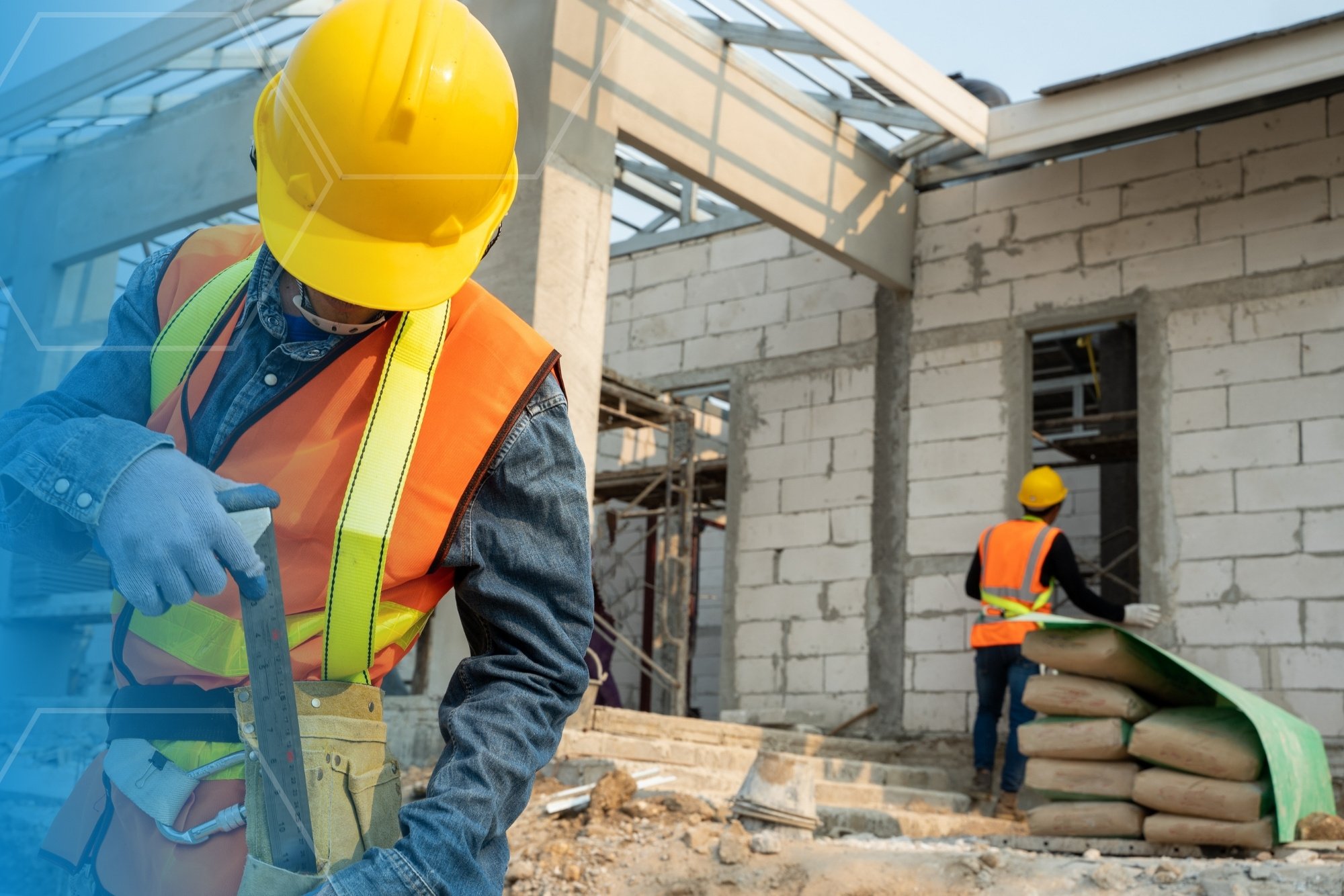
Minimize Waste and Loss in Your Ready-Mix Concrete Timeline
Inefficiencies in ready-mix concrete production and dispatching lead to material waste, production delays, unhappy customers, and financial losses. Factors like batching inaccuracies, scheduling mismanagement, equipment failures, and poor route optimization create bottlenecks that drive up costs and reduce profitability. Your ready-mix concrete timeline has to ensure high-quality output, cost savings, and smooth operations from batching to delivery to reduce the risk of waste eating into profits. Technology developed specifically for the concrete industry helps ready-mix producers streamline workflows, enhance operational efficiency, and reduce waste at every stage of production.
Let’s take a look at some common ready-mix concrete timeline issues and what you can do to prevent them from damaging your bottom line.
Where Waste Happens in the Ready-Mix Concrete Timeline
An NIH report titled, “Waste Generation from the Production of Ready-Mixed Concrete” clarified concrete plant waste, determining that 3% of all produced volume returns to the plant. The main cause of concrete leftovers was associated with overordering and corresponded to 58% of this volume.
Waste also often occurs in operations and dispatching. Identifying inefficiencies within your ready-mix concrete timeline and correcting them with technology is the key to reducing it.
Reduce Operational Inefficiencies at Your Ready-Mix Concrete Plant
Batching Inaccuracies: Manual entry errors, outdated batch control systems, and lack of real-time monitoring result in mix inconsistencies and material waste. These inaccuracies lead to rejected loads, increased production costs, and delayed orders. The loss associated with each incorrect batch is compounded by wasted raw materials and unnecessary labor.
Precision in concrete batching reduces material waste. Modern batch control systems use real-time sensors and AI-powered automation to ensure accurate water-cement ratios and proper mix proportions. This minimizes errors, reduces rejected loads, and enhances mix uniformity, ultimately optimizing the ready-mix concrete timeline. Companies using automation enjoy a significant decrease in material overuse and an increase in overall productivity.
Poor Material Handling and Storage: Concrete materials have a limited shelf life, and improper storage can lead to contamination or deterioration. Over-purchasing raw materials results in excess stock that may go unused, while under-purchasing causes production halts and delayed deliveries. Automated inventory tracking can prevent these ready-mix concrete timeline issues by maintaining optimal stock levels and reducing reliance on manual tracking, where a single input error can cause the waste of an entire batch.
Smart inventory management systems powered by IoT sensors allow real-time tracking of material levels and usage trends, enabling proactive purchasing strategies and reducing material waste. When integrated with AI-driven inventory optimization and demand forecasting, these systems automatically make adjustments to prevent overstock and shortages.
Equipment Downtime and Malfunctions: Unexpected equipment failures in batching plants, conveyors, or silos bring production to a standstill. IoT-enabled predictive maintenance solutions help plants proactively address maintenance needs, minimizing costly downtime and waste by detecting early signs of wear and tear and allowing operators to schedule maintenance before a breakdown occurs. Predictive maintenance reduces unplanned downtime, ensuring that production remains uninterrupted, and waste is minimized.
Automated diagnostics provide real-time updates on equipment performance, helping managers make informed decisions about repairs and replacements before they escalate into major failures. Integrating regular maintenance schedules with predictive analytics ensures each piece of equipment operates at peak efficiency, preventing unnecessary breakdowns that cause production delays and excess material waste. Machine learning algorithms analyze operational data to predict component failures before they happen, reducing emergency repairs and operational downtime.
Overcome Dispatching and Scheduling Challenges
Order and Delivery Mismanagement: Without real-time scheduling updates, it's easy for plants to overcommit or to underutilize resources. Either scenario creates mismanaged orders that disrupt ready-mix concrete timeline with excessive truck turnaround times, inefficient batching, and increased fuel costs. Cloud-based dispatching solutions allow for dynamic order adjustments, improving scheduling efficiency and reducing unnecessary expenses.
AI-driven demand forecasting tools further enhance dispatch accuracy, allowing ready-mix plants to anticipate order trends and adjust batching schedules accordingly to maximize efficiency. Predictive analytics reduce underutilization of trucks, ensuring that vehicles are dispatched optimally.
Traffic and Route Inefficiencies: Poor route planning causes trucks delays and concrete batches that set before arrival. AI-driven route optimization tools help navigate traffic congestion and determine the most efficient delivery routes, reducing the likelihood of wasted loads. These cutting-edge systems integrate truck telematics, real-time GPS data, weather conditions, and job site readiness to ensure smooth and efficient deliveries. Geofencing and automated traffic analysis tools further streamline routing, ensuring that deliveries arrive at optimal times without unnecessary stops or detours.
Communication Gaps: Lack of real-time coordination between ready-mix batching plant, drivers, and job sites leads to confusion, rescheduling issues, and wasted resources. Digital ticketing and mobile communication platforms improve coordination and reduce delays. These systems enhance collaboration and minimize costly miscommunications by providing all stakeholders with access to live updates.
Automated job site notifications and mobile-friendly order tracking systems provide visibility to contractors, helping them better prepare for deliveries and avoid last-minute complications. Dispatch managers are empowered to rapidly adjust schedules and optimize real-time communication with field teams.
Optimize Your Ready-Mix Concrete Timeline with Sysdyne
Concrete producers are experiencing difficulties attracting and retaining workers, especially among mixer drivers. The short staffing issue is having a negative impact on ready-mix concrete producers. The experts at MIT encourage companies to find relief by optimizing their timelines with technology, saying, "A 1% change in productivity can provide up to a 1% increase in expected annual net revenue. That means that a firm could invest more than 5% of their expected annual net revenues in a new technology for every 1% gain in productivity and still come out ahead.”
Integrating Sysdyne’s cutting-edge technology into your plant’s production and dispatching will optimize your ready-mix concrete timeline.
The leader in cloud-native concrete batching systems, CloudBatch is designed to help ready-mix producers streamline operations, reduce waste, and maximize profitability. It’s even more powerful when combined with ConcreteGO concrete dispatch software and iStrada concrete delivery management software.
What Makes Sysdyne Different?
- Real-Time Batch Monitoring: Provide live updates on batching operations, ensure precise mixing, and minimize waste.
- Automated Scheduling: Optimize truck utilization and plant output while reducing errors and inefficiencies.
- AI-Driven Route Optimization: Use data-driven insights to determine the most efficient delivery routes, cutting fuel costs and preventing delays.
- Predictive Maintenance: Employ IoT-enabled sensors to anticipate equipment failures, minimizing downtime and production halts.
- Seamless Cloud Integration: Manage and adjust batching processes from any location with any internet-enabled device, increasing overall flexibility.
- Integrated Performance Dashboard: Consolidate data into easy-to-read insights, to make informed and real-time decisions that optimize your ready-mix concrete timeline.
- Smart Inventory Management: Monitor raw material usage in real-time, preventing over-ordering and shortages.
- Enhanced Customer Communication: Automate SMS delivery notices, improving coordination and reducing unnecessary calls to dispatch.
- Enhanced Reporting Capabilities: Generate detailed reports on production, performance, and efficiency to help identify areas for improvement.
- Customization and Scalability: Every Sysdyne implementation is designed to meet the specific needs of the operation it supports, allowing for maximum flexibility in configuration and integration with platforms already in use.
- Knowledgeable Onshore Support: Get expert assistance when you have questions about using the platform to solve operational challenges quickly and efficiently.o
Take the Next Step
The future of ready-mix concrete production is rooted in new technology that improves efficiency with automation. Ready-mix concrete producers who opt for technology that integrate smart batching systems, AI-powered dispatching, and predictive maintenance tools minimize waste, cut costs, and enhance their production timelines.
Ready to learn how to transform your plant operations with Sysdyne? Schedule a demo today.