Gestión de entrega completamente integrada de iStrada®, productores de hormigón y clientes: una combinación ganadora
Hercules Concrete está llevando el servicio al cliente al siguiente nivel utilizando la plataforma de colaboración con el cliente en línea de iStrada. Como parte del paquete iStrada de rastreo de camiones con GPS con todas las funciones, los productores de concreto ahora pueden compartir información crítica sobre trabajos y entregas con sus clientes en línea utilizando cualquier dispositivo móvil para ahorrar tiempo y generar confianza mientras promueven la transparencia.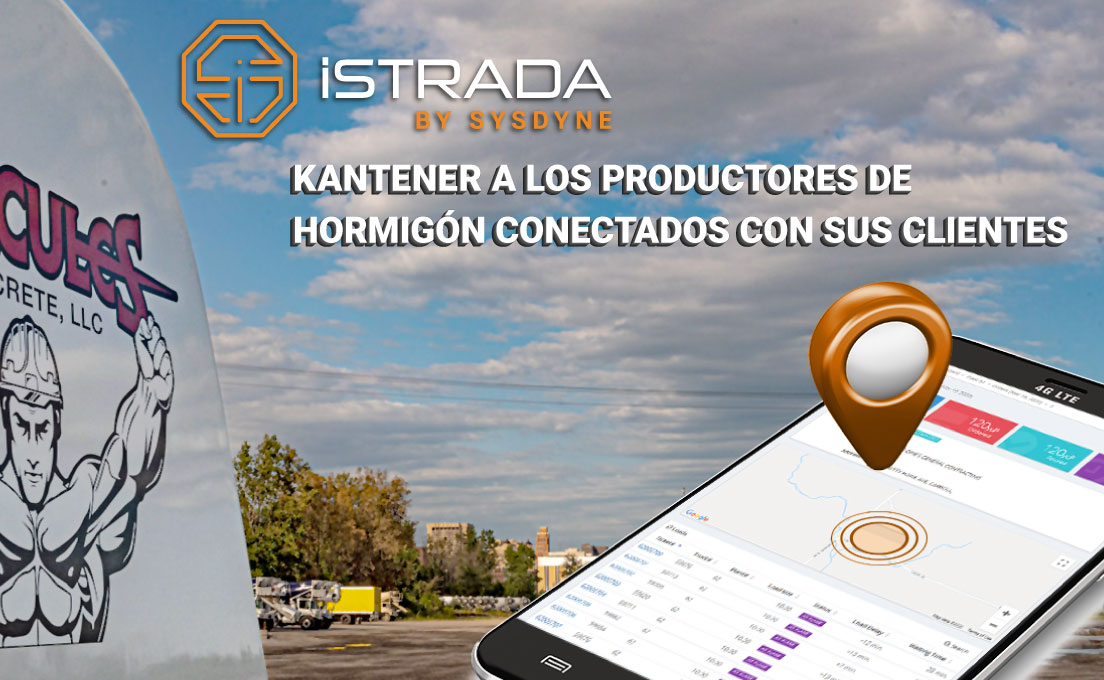
Digital Transformation in the Construction Industry: Job Site Technology That Is Here to Stay
The construction industry has been integrating technology at a growing rate over the past decade. In 2020, like many other industries, the adoption of technology was significantly accelerated on construction job sites, and some of the changes are here to stay. The benefits of cloud-based job site technology are constantly growing and will continue to shape the way we work for many years to come.
Throughout the COVID-19 crisis, years of technological change were compressed into months. While some contractors were able to adapt quickly to the vastly altered landscape in 2020 because they had already been using cloud-based software, others were held back by drastic changes in operation. Now that this shift has taken place, tech firms anticipate the trend to continue.
“The point here is that businesses have realized that investing in technology is not something that you should do in a reactive way, but something that you proactively look at – This is not just about being distinguished.”
COVID-19 has standardized the remote work environment, and made it a must-have to be in the cloud. Although the pandemic was disruptive for the current clients of ERP developer Acumatica, it was not crippling. “They were able to ask their employees to basically, ‘Take your laptop and work from home starting tomorrow,’” vice-president of Platform Strategy at Acumatica.
At the same time, many of those who lacked the proper tech resources were able to easily move from their legacy systems to platforms such as Acumatica to keep their job sites going and dialed in by their remote employees.
Similar adoption patterns were seen by construction management software provider InEight as the need to communicate remotely bumped up.
The chief product officer of InEight said that the pandemic intensified what had been a “creeping” movement towards digitization in construction.
“The pandemic was kind of an urge to urge them into those changes, but now that they’re there and they see all the benefits of it, I don’t see them moving off of it”
About a year into the pandemic – and at least a few months until an operating environment resembling normal starts to re-emerge, the tech tools contractors and those in construction implemented have already been embraced, making it very unlikely for them to return to their pre-pandemic methods of operation.
More specialized segments of the tech market have also seen rapid uptake during the pandemic.
With few areas requiring as much attention as health and safety, the co-founder and CEO of SafetyTek says the company has more users and daily app interactions than ever. The firm’s paperless safety management platform helps contractors collect data from the field, allowing health and safety managers to create custom forms to meet disparate reporting requirements in different jurisdictions.
Along with diverting the process to the cloud to minimize staff on-site, SafetyTek’s solution helped tackle one of the novel health challenges COVID brought to the surface.
“If you get injured on-site, you can go home and go to your family and not worry about harming them, but if you get a virus on-site, you can go home and spread that – That is what’s really put health and safety on a pedestal, I would say, especially in the construction area where most people are a little more cautious now about how they interact with folks on-site.”
Like their counterparts in other operational roles, health and safety managers were acting from a reactionary position in 2020. In the coming months, he expects to see that change.
“2021 needs to be the year where we can take a calibrated approach to implementing solutions so we don’t get put in this position again,” he said.
In addition to logging mandatory safety forms and related information, SafetyTek is also coaching clients on how to make the best of their data. With metrics such as incidents and near misses on-hand, contractors can glean insight on how to better manage their safety programs.
Likewise, InEight is looking to help the industry utilize the stores of information now at its disposal.
“We’ve got this wealth of data sitting there, so now the opportunity becomes how do we turn that information into something that makes everybody on the team smarter,” said the chief product officer.
Driven in part by the pandemic, digital transformation throughout construction has likely now moved past its halfway point. The industry’s use of artificial intelligence and machine learning to increase productivity on job sites, on the other hand, remains in its infancy.
Using both industry and company-specific benchmarking to optimize job sites will keep tech firms growing throughout construction in 2021 and beyond. This more nuanced approach to data will also help construction overcome a number of the barriers contributing to its so-called “productivity gap.”
Builders should also integrate the lessons learned during 2020 into their post-pandemic plans. In particular, as AI and other new tools like sensors and robotics filter into construction, contractors need to be willing to act quickly.
“Traditionally, if you go into a process of choosing a new platform and technology, it’s a large committee involved and it’s a decision by committee and it takes forever. Instead, as the pandemic took hold, construction companies were very scrappy about making adjustments. One of the key takeaways from this is that you could actually move fast – moving fast doesn’t mean you’re losing control.”
Link to original article