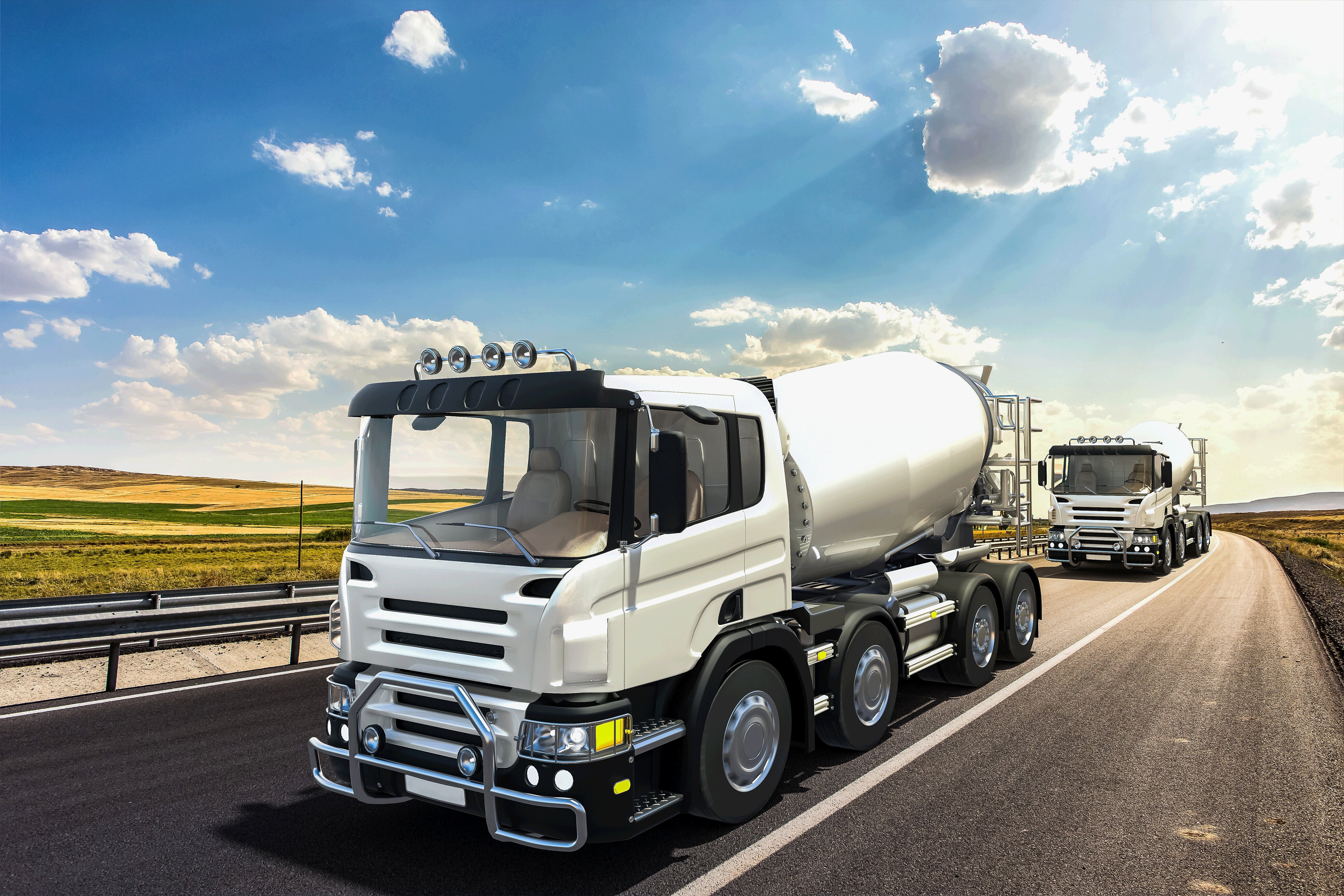
5 Tips for Optimizing Routes and Schedules with Trucking GPS Tracking Systems
5 Tips for Optimizing Routes and Schedules with Trucking GPS Tracking Systems
If you're in the concrete business, you know timing is everything. Getting deliveries right is crucial for keeping projects on track. One of the best ways to boost your efficiency is is through the use of trucking GPS tracking system. These tools give you real-time data to help you optimize routes and schedules so you can do your part to make every project as successful as possible.
GPS tracking systems facilitate seamless communication by providing real-time updates and alerts. Dispatchers can send immediate instructions to drivers, informing them of route changes, delivery priorities, or any other critical information. This continuous flow of information helps get everyone on the same page and prevents delays.
Let's dive into five tips to make the most out of trucking GPS tracking systems.
1. Leverage Real-Time Data for Enhanced Route Planning
Real-time GPS tracking is the cornerstone of an effective route optimization strategy. By equipping your fleet with GPS tracking devices, you can see exactly where each truck is at any moment. This lets dispatchers make quick decisions, like rerouting trucks to avoid traffic jams or road closures.
By accessing live traffic updates, weather conditions, and road closures, concrete delivery companies can adjust routes on the fly to avoid delays and minimize disruptions.
Utilize GPS for Trucks to Avoid Traffic Congestion
If an accident blocks your driver’s main route, dispatchers can instantly redirect them to a better path. This quick response helps keep deliveries on time and reduces downtime, making your operations more efficient (and customers happier).
GPS systems designed specifically for concrete trucks offer advanced features to navigate around traffic congestion. By picking the fastest and most efficient paths, you save time, cut down on fuel consumption, and meet your delivery deadlines more consistently. Plus, less idle time means less wear and tear on your vehicles. This proactive approach to traffic management helps maintain a smooth flow of operations and less headaches for your drivers and customers.
Implement a Truck Tracking System for Dynamic Scheduling
Unlike static scheduling, which sets fixed schedules in advance, dynamic scheduling continuously adjusts based on various factors such as traffic conditions, weather, availability of resources, and changes in demand. It allows for flexible and adaptive planning that responds to changing conditions on the road.
Truck tracking systems provide real-time updates on vehicle locations and traffic conditions, ensuring your schedules are always optimized. This flexibility means you can swiftly handle unexpected events and keep your operations running smoothly.
2. Optimize Efficiency with Truck Tracking Apps
The concept of a tracking app is likely going to be met with some concern or pushback from drivers. They might feel like their every move is being monitored, which can feel intrusive.: Real-time tracking can add pressure to meet deadlines and optimize routes, and constant monitoring can feel like micromanagement, reducing their sense of autonomy and trust from their employers.
However, the right truck tracking system can actually have tremendous benefits for drivers in terms of safety and even resolving disputes. Tracking systems often come with features like route optimization and real-time traffic updates, helping drivers avoid dangerous areas and reduce the risk of accidents. Because there is a there is a clear record of where the truck has been and how it’s been operated, these apps are useful for resolving disputes and ensuring accountability.
These systems help streamline operations by providing the most efficient routes, reducing fuel consumption and travel time. A truck tracking app can play a crucial role in monitoring and optimizing fuel. By tracking factors such as idling time, speed, and route efficiency, these apps help identify areas where fuel consumption can be reduced. Implementing a truck tracking app can lead to significant cost savings and environmental benefits by promoting more fuel-efficient driving practices.
Monitor Driver Behavior to Reduce Fuel Consumption
Optimizing routes and schedules isn’t just about finding the quickest path; it’s also about ensuring that drivers are performing at their best. GPS tracking systems offer features to monitor driver behavior, such as speed, braking patterns, and idling times. By keeping an eye on these metrics, you can identify areas where drivers might need additional training or guidance.
For example, excessive speeding not only poses safety risks but also increases fuel consumption. By addressing this behavior, you can improve fuel efficiency and ensure safer driving practices overall.
Plan Fuel Stops More Effectively
By monitoring factors like idling time, acceleration patterns, and speed, concrete delivery companies can identify behaviors that lead to excessive fuel consumption. Providing feedback and training to drivers based on this data can result in better driving habits, ultimately reducing fuel costs and extending the lifespan of the vehicles.
Effective fuel stop planning is crucial for minimizing detours and downtime. GPS tracking systems can assist in finding the most efficient fuel stops along the route, ensuring that trucks refuel at optimal locations without unnecessary deviations. This helps maintain a smooth, continuous journey.
3. Improve Delivery Times with Advanced Trucking Software Dispatch
At the end of the day, what customers want is reliable products and on-time service. Trucking software dispatch systems play a vital role in improving delivery times so concrete is delivered when and where people need it. From order to finally delivery, the right trucking software dispatch system helps reduce wait times and ensures that your trucks are always ready for their next delivery.
Automate Dispatch Processes
These systems use automation to reduce manual human errors and save valuable time. By incorporating trucking software dispatch into their operations, concrete companies can enhance communication between dispatchers and drivers and ensure timely deliveries.
Enhance Communication Between Dispatchers and Drivers
Good communication between dispatchers and drivers is essential for smooth operations. Trucking software dispatch systems provide tools that facilitate real-time communication, allowing dispatchers to relay important information quickly and accurately. This keeps drivers informed about route changes, delivery instructions, and any other critical updates.
4. Increase Fleet Utilization with Truck Demand Forecasting
Truck demand forecasting is a powerful tool for making the most of your fleet. By analyzing historical data and predicting future demand, concrete delivery companies can make informed decisions about fleet size and resource allocation. This proactive approach helps match fleet capacity with demand, leading to cost savings and better resource management.
Analyze Historical Data for Accurate Demand Predictions
Real-time tracking is great, but analyzing historical data is also crucial for long-term route optimization. GPS tracking systems collect tons of data, including travel times, fuel consumption, and traffic patterns. By examining this data, you can spot trends and inefficiencies in your delivery routes, allowing for strategic adjustments to avoid peak traffic periods and reduce travel time and fuel costs.
For example, you might find that certain routes are always congested at specific times of the day. With this knowledge, you can adjust your schedules to avoid these peak periods, saving time and fuel. Historical data analysis also helps identify the most efficient routes, which can be implemented across your fleet to standardize and streamline operations.
Adjust Fleet Size Based on Demand Fluctuations
Adjusting your fleet size based on demand fluctuations is key to keeping operations cost-effective. Truck demand forecasting lets companies scale their fleet up or down as needed, ensuring they have the right number of trucks on the road at all times. This flexibility leads to better resource management and significant cost savings.
5. Discover Sysdyne’s GPS Tracking Solutions
The concrete industry often faces big challenges in managing logistics and ensuring smooth collaboration among stakeholders. Sysdyne has developed a comprehensive truck tracking and management solution to tackle common challenges before they turn into major issues.
iStrada offers real-time tracking, automatic updates, and electronic delivery of tickets, greatly improving the overall client-business interaction experience.
GPS Truck Tracking
- Precise truck tracking with turn-by-turn navigation assistance
- Optimization of truck routes to avoid obstacles like low bridges
- Ensuring safer and more efficient deliveries
E-Ticketing
- Automatic updates to truck status, water content, and inspection results
- Paperless ticketing system with batch weights and electronic signatures
- Easy emailing of tickets directly from the driver’s app
Time and Attendance
- Comprehensive management of drivers' and hourly employees' time and attendance
- Includes driver callout functionality for efficient communication and coordination
With a fully integrated cloud-native software suite, we cover the entire spectrum of concrete operations, including sales, production, and delivery. By leveraging the latest in technology, our systems provide real-time data, dynamic scheduling capabilities, and advanced tracking features to optimize routes, improve fuel efficiency, and enhance overall productivity.
Schedule a demo of our truck tracking system today.