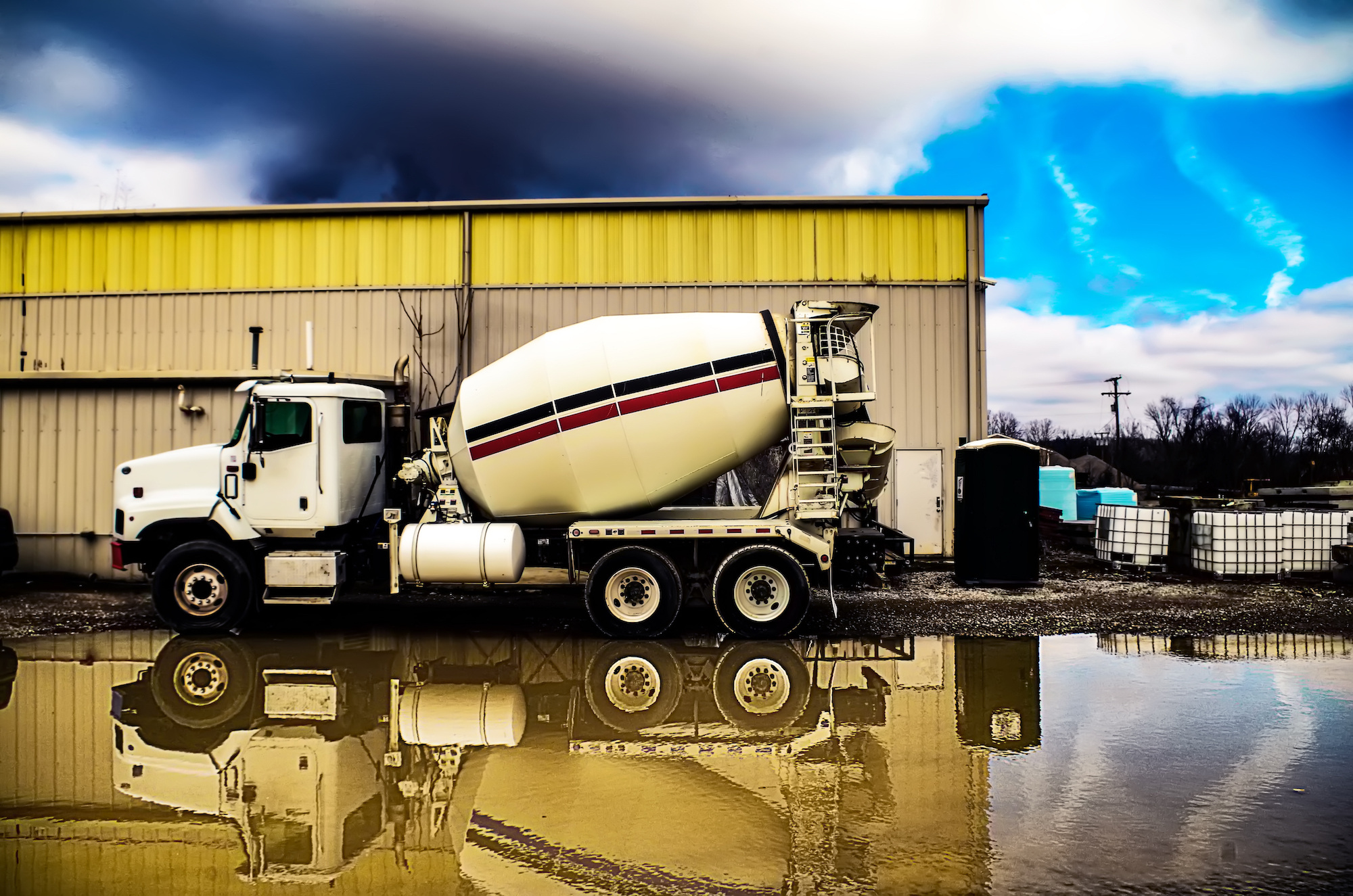
From Dispatch to Delivery: How Real-Time Insights Improve Concrete Operations
When tracing the journey of concrete from dispatch to delivery, access to real-time information at every step is critical. From order placement, batching, and loading, to delivery and post-delivery tracking—concrete companies can optimize operations, reduce costs, and enhance the quality of their service. These insights improve efficiency and ensure timely deliveries, better quality control, and higher-quality service.
Why Real-Time Insights Are Crucial for Concrete Dispatch Management
Concrete companies face challenges when dispatching without real-time data, including:
- Delivery delays
- Miscommunication
- Inefficient use of resources
These issues lead to all sorts of consequences that negatively impact operations (higher fuel consumption, downtime, and lower productivity, to name a few). Real-time insights change the game by enabling dispatchers to schedule deliveries with greater accuracy, make on-the-fly adjustments, and gain greater visibility and oversight into each step of the process.
The Impact of Real-Time Scheduling and Route Optimization on the Concrete Industry
Using real-time data, concrete dispatchers can schedule more efficiently, cutting down on idle times and ensuring trucks are ready when needed. Additionally, live data helps optimize delivery routes to avoid traffic, reduce fuel consumption, and reduce delays. This level of precision in dispatching improves overall delivery speed and customer satisfaction, while also ensuring concrete mixes maintain their quality by arriving on time.
Let’s take a look at the journey of concrete from dispatch to delivery and explore how real-time insights at each stage can significantly optimize operations and enhance service quality.
1. Order Placement and Scheduling
The concrete journey begins when an order is placed. This is the stage where project requirements, delivery times, and concrete specifications are outlined. Traditionally, managing multiple orders manually or through outdated systems can lead to scheduling conflicts, delays, and miscommunication between project managers.
Real-Time Insights:
By using real-time, concrete production and dispatch management software, like Sysdyne’s ConcreteGO, dispatchers can streamline order entry and scheduling. The system provides a live view of plant production, fleet availability, and current traffic conditions, ensuring the most efficient scheduling and preventing over-commitment. Real-time insights also allow for immediate adjustments in response to urgent orders or sudden changes in demand, optimizing fleet allocation and scheduling accuracy.
2. Concrete Batching
Once the order is scheduled, the batching process begins at the plant. The exact mix design is crucial to ensuring the quality and strength of the concrete. Variations in mixing time, water content, or cement ratios between mix designs can lead to compromised quality and costly rework.
Real-Time Insights:
Advanced batching systems like CloudBatch from Sysdyne provide real-time monitoring and control over the batching process. Operators can ensure consistent mix quality by receiving real-time data on water-cement ratios, batch weights, and mix time. If there's an issue with the mix, the system immediately alerts operators, allowing them to correct it before it becomes a costly problem. This not only ensures the quality of the concrete but also reduces material waste and batch rejections.
3. Loading the Concrete into Trucks
Once the concrete is batched, it’s loaded into mixer trucks for delivery. Ensuring trucks are loaded efficiently and dispatched on time is critical to maintaining the quality of the mix during transportation.
Real-Time Insights:
Real-time fleet management tools allow dispatchers to see which trucks are ready and available for loading, reducing idle time at the plant. Tools like iStrada provide real-time visibility into truck status, allowing for better coordination between batch plant operators and dispatchers. This ensures that trucks are dispatched promptly after loading, reducing waiting times and ensuring concrete freshness when reaching the job site.
4. On-the-Road: Route Optimization and Concrete Monitoring
As the truck travels to the job site, it's crucial to monitor both the route and the condition of the concrete in the mixer. Delivery is often one of the most challenging stages in concrete operations. Without real-time monitoring, unexpected traffic, weather changes, or delays can result in subpar concrete quality. With live concrete delivery tracking, companies can ensure that trucks remain on schedule and that the quality of the mix is preserved throughout transit.
Real-Time Insights:
Real-time GPS tracking and route optimization are vital during this phase. Dispatchers can monitor truck locations in real-time, adjusting routes based on traffic, accidents, or road conditions. This minimizes delivery delays and ensures that the concrete arrives within its usable timeframe. Real-time monitoring also helps maintain mix consistency by tracking the drum’s rotation speed and water content, preventing issues like slump loss during transit.
5. Arrival at the Job Site
Upon arrival at the job site, the quality of ready mix for the concrete needs to be confirmed, and the truck must be ready to pour. If the concrete mix is off-spec, it could lead to delays and increased costs due to rework or rejected loads.
Real-Time Insights:
Real-time concrete quality control systems monitor the mix right up until the point of delivery. These systems track parameters such as water-cement ratio, slump, and temperature, ensuring that the concrete meets the required specifications. If adjustments are needed, they can be made on-site before pouring, minimizing the risk of rejections and ensuring the customer receives high-quality concrete.
6. Delivery Confirmation and Documentation
Once the concrete is delivered, documentation like delivery tickets and inspection reports must be completed. Traditionally, this process has been paper-based and prone to errors or delays in record-keeping.
Real-Time Insights:
With solutions like iStrada’s e-ticketing, the delivery process is fully digitized. The driver can submit electronic tickets that are automatically updated with the truck’s status, water content, and batch weights, ensuring accurate, real-time records of each delivery. This streamlines communication between the delivery team and the customer, reducing disputes and building trust through transparency.
7. Post-Delivery Monitoring and Customer Satisfaction
Even after the concrete has been delivered, real-time data management insights continue to add value. Monitoring the status of the remaining fleet, addressing customer feedback, and analyzing operational efficiency are critical to ensuring ongoing improvement.
Real-Time Insights:
Post-delivery, real-time data allows dispatchers to monitor the fleet’s return and prepare trucks for the next round of deliveries. This data also provides valuable feedback for future scheduling and routing optimizations. Customers can track deliveries in real-time and access all the documentation digitally, improving communication and overall satisfaction. Additionally, real-time driver performance and metrics help concrete companies analyze KPIs, identify bottlenecks, and implement continuous improvement strategies.
Optimizing Fleet and Equipment Utilization with Real-Time Insights
Maximizing fleet productivity is key to reducing costs and keeping things running smoothly. Real-time concrete fleet management tools help track vehicle performance, fuel usage, and maintenance needs, allowing concrete producers to optimize their resources cost-effectively. This proactive management increases the number of loads delivered and reduces truck wear and tear.
Predictive Maintenance with Real-Time Data
By leveraging real-time data, concrete companies can adopt a predictive maintenance approach, identifying potential equipment issues before they cause downtime. Early detection of engine faults or worn-out components helps ensure that fleets operate smoothly and extend the lifespan of trucks, pumps, and other essential equipment.
Ensuring Consistency in Concrete Mix During Delivery
Quality control allows companies to monitor slump loss, water-cement ratio, and concrete temperature for changes, helping prevent issues before the concrete arrives at the job site. This level of oversight reduces the risk of load rejections, minimizing wasted materials and cutting costs. Having access to real-time data also allows supervisors to make adjustments, such as tweaking truck speeds or rotation rates, to maintain consistency in the mix.
How Real-Time Insights Improve Decision-Making for Concrete Operations
Real-time data enables concrete operations managers to make smarter, data-driven decisions. Whether it's adjusting delivery routes in response to traffic conditions or reallocating resources during peak demand, having immediate access to actionable data helps businesses respond more efficiently. Analyzing operational data in real time allows companies to fine-tune processes and improve their bottom line.
Leveraging Data Analytics to Boost Efficiency
Tracking key performance indicators (KPIs) like delivery times, fuel consumption, and equipment uptime through real-time data offers invaluable industry insights. Companies can identify trends, uncover inefficiencies, and implement continuous improvement initiatives to boost productivity and reduce operational costs.
The Role of Real-Time Insights in Enhancing Customer Service
In today's competitive market, providing exceptional customer service is crucial to profitability. Real-time concrete delivery tracking offers transparency by keeping customers informed at every stage of the process. Providing customers with live updates on their deliveries reduces inquiries, minimizes complaints, and builds trust, ultimately enhancing satisfaction.
Real-Time Order Tracking for Customer Communication
Real-time order tracking systems allow the concrete industry and customers to follow their deliveries in real-time. They can see when their concrete is mixed when it leaves the plant, and when it will arrive at the job site. This visibility into the delivery process strengthens the relationship between concrete companies and their clients by fostering clear, consistent communication.
How Sysdyne’s Solutions Support Real-Time Concrete Operations Management
Sysdyne’s suite of cloud-native software solutions provides the real-time insights that concrete companies need to thrive. From GPS truck tracking to automated dispatch and delivery tracking, Sysdyne’s cloud-based platform solutions are designed to optimize every stage of concrete operations management. By integrating seamlessly with existing systems, Sysdyne makes adopting real-time data technology straightforward and scalable.
The Benefits of Choosing Sysdyne for Concrete Operations
Sysdyne's solutions are easy to implement and customize, allowing concrete producers to tailor the system to their specific needs. With Sysdyne, businesses benefit from ongoing support, regular updates, and a commitment to helping concrete producers achieve their operational goals. Switching to Sysdyne means improved efficiency, lower costs, and greater visibility across the entire supply chain.
Sysdyne offers the technology and expertise to make real-time insights a cornerstone of your concrete operations. Ready to optimize your dispatch and delivery processes? Explore Sysdyne’s ConcreteGO dispatch management system to learn more.