Industry 4.0 represents the fourth industrial revolution
…but what technologies are transforming the manufacturing sector today?
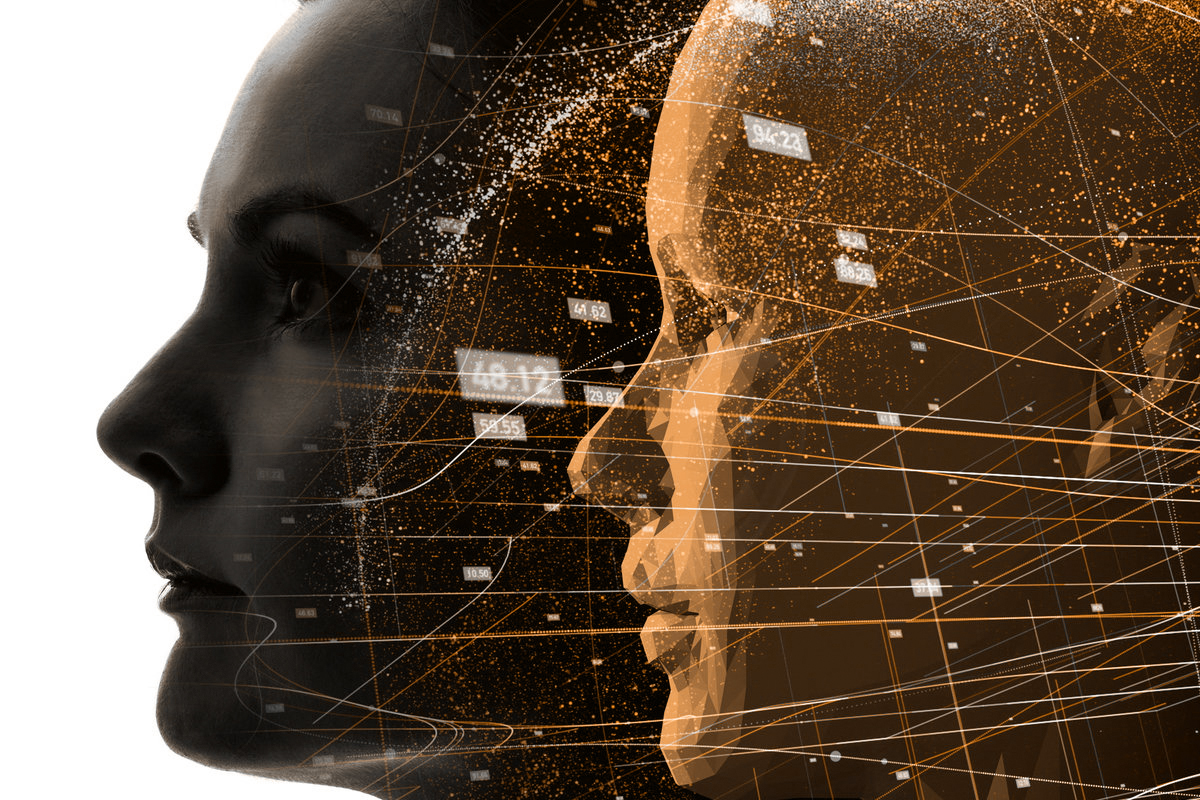
Why are these technologies essential to Industry 4.0?
A hallmark of Industry 4.0 is the speed with which results can be seen using the data generated and collected and the degree to which this data affects users.
Digital Twin
Digital Twins are presented as a disruptive technology in analyzing and simulating industrial processes, helping to maximize the benefits of plant digitization – a transformation in which many companies have already begun, and which will intensify in the coming years.
Digital Twins are live digital representations of machines, devices, and processes that are connected to the real system they represent through “Cyber-Physical Systems” (CPS). By using them, new solutions can be tested in shorter periods of time and at a lower cost.
Edge Computing
The difference between the third and fourth industrial revolutions is the use and accumulation of data. In an increasingly competitive and transnational environment, we need a tool that allows us access to production information at any moment, regardless of location.
Edge computing enables smooth handling of the large amount of data that is managed, as it is also possible to process information at the edge of the network, close to the machine where the data is produced, thus reducing for example the processing latency. Further, since the information has already been processed, the data center receives smaller volumes, thus saving bandwidth.
Additive Manufacturing
Research on 3D printers using new materials will change manufacturing processes and systems in ways we never imagined. This will result in a significant reduction in development costs for prototypes or short series.
Thanks to 3D printing, it is possible to print any element in various shapes and sizes in a totally personalized way with many materials and to create models and functional parts even in small series at very low costs.
5G
During the production process, 5G can speed up information transfer and increase automation. It will then be possible to improve the performance of autonomous machines by utilizing “Network Slicing” — the capability for 5G to divide a network into smaller segments.
The Network Slicing will adjust connectivity to individual needs and situations. By combining 5G and industrial automation, more network resources can be allocated to machines. The automated sector of the industry will then benefit greatly from 5G.
Artificial Intelligence
The Industry 4.0 framework cannot be reduced solely to the technologies listed above.
Artificial intelligence (AI) is the driving force behind the internal changes within factories. In a production environment, AI allows machines to communicate with each other and, most importantly, to learn from various situations, resulting in greater efficiency and reduced costs.
The use of artificial intelligence in the automotive sector, however, will lead to the exponential growth of driverless systems, and this will negatively impact the industry.
Cybersecurity
Let’s not forget that cybersecurity involves protecting information and systems against major cyber threats, such as cyberterrorism or cyber espionage.
With all the cyber threats evolving rapidly and continuously, maintaining cybersecurity strategy and operations is a great challenge for private companies.