The industry needs to change; here’s how to manage it.
The construction industry is ripe for disruption. Large projects across asset classes typically take 20 percent longer to finish than scheduled and are up to 80 percent over budget (Exhibit 1). Construction productivity has declined in some markets since the 1990s (Exhibit 2); financial returns for contractors are often relatively low—and volatile. Exhibit 1Exhibit 2
While the construction sector has been slow to adopt process and technology innovations, there is also a continuing challenge when it comes to fixing the basics. Project planning, for example, remains uncoordinated between the office and the field and is often done on paper. Contracts do not include incentives for risk sharing and innovation; performance management is inadequate, and supply-chain practices are still unsophisticated. The industry has not yet embraced new digital technologies that need up-front investment, even if the long-term benefits are significant (Exhibit 3). R&D spending in construction runs well behind that of other industries: less than 1 percent of revenues, versus 3.5 to 4.5 percent for the auto and aerospace sectors. This is also true for spending on information technology, which accounts for less than 1 percent of revenues for construction, even though a number of new software solutions have been developed for the industry.
Exhibit 3
Technical challenges specific to the construction sector have a role in the slow pace of digitization. Rolling out solutions across construction sites for multiple sectors that are geographically dispersed—compare an oil pipeline, say, with an airport—is no easy task. And given the varying sophistication levels of smaller construction firms that often function as subcontractors, building new capabilities at scale is another challenge. However, none of this is going to get easier. Projects are ever more complex and larger in scale. The growing demand for environmentally sensitive construction means traditional practices must change. And the shortage of skilled labor and supervisory staff will only get worse. These are deep issues that require new ways of thinking and working. Traditionally, the sector has tended to focus on making incremental improvements, in part because many believe that each project is unique, that it is not possible to scale up new ideas, and that embracing new technologies is impractical. The McKinsey Global Institute estimates that the world will need to spend $57 trillion on infrastructure by 2030 to keep up with global GDP growth.1 This is a massive incentive for players in the construction industry to identify solutions to transform productivity and project delivery through new technologies and improved practices. In this report, we consider five ways the industry can transform itself over the next five years.
Disrupting construction: Five big ideas
None of these five ideas is futuristic or even implausible. All are grounded in innovations that are applicable to the construction sector and that are either being deployed or prototyped. In short, they are practical and relevant. Moreover, they are designed to work together to deliver greater impact (Exhibit 4). Exhibit 4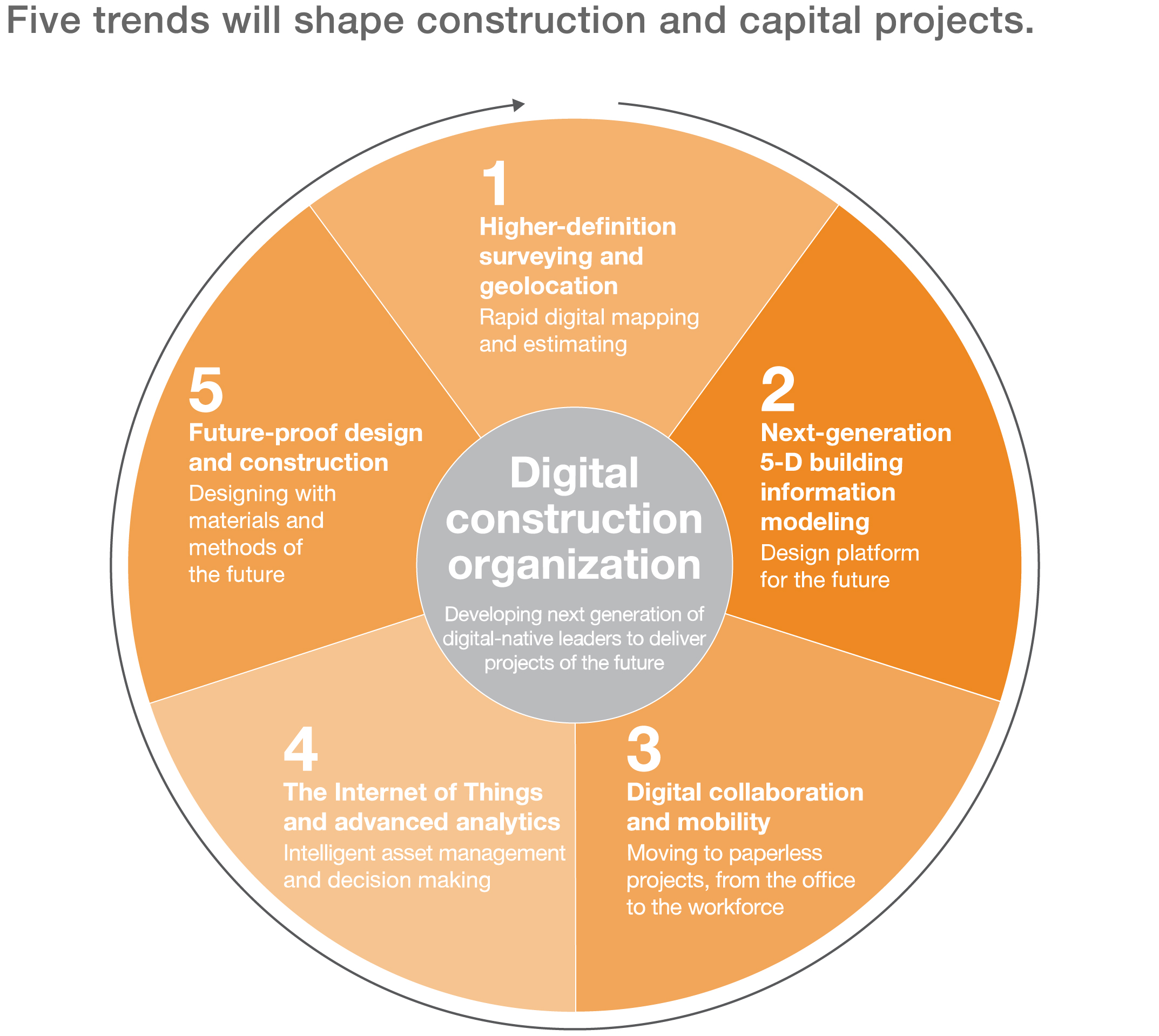
Digital collaboration and mobility
Process digitization means moving away from paper and toward online, real-time sharing of information to ensure transparency and collaboration, timely progress and risk assessment, quality control, and, eventually, better and more reliable outcomes. One reason for the industry’s poor productivity record is that it still relies mainly on paper to manage its processes and deliverables such as blueprints, design drawings, procurement and supply-chain orders, equipment logs, daily progress reports, and punch lists. Due to the lack of digitization, information sharing is delayed and may not be universal. Owners and contractors therefore often work from different versions of reality. The use of paper makes it difficult to capture and analyze data; that matters because in procurement and contracting, historical performance analytics can lead to better outcomes and risk management. Mismanaged paper trails also routinely spur disagreements between owners and contractors on such matters as construction progress, change orders, and claims management. Finally, paper trails simply take more time. Owners and contractors are beginning to deploy digital collaboration and field-mobility solutions (Exhibit 7). A large global construction firm recently announced a joint development agreement with a software provider to develop a cloud-based, mobile-enabled field-supervision platform that integrates project planning, engineering, physical control, budgeting, and document management for large projects. Several large project developers have already successfully digitized their project-management workflows.
Exhibit 7 Exhibit 8
The Internet of Things and advanced analytics By measures such as the number of people, the profusion of construction equipment, and the amount of work going on at the same time, project sites are getting denser. They now generate vast amounts of data, a majority of which is not even captured, let alone measured and processed. The Internet of Things is a reality in many other sectors; sensors and wireless technologies enable equipment and assets to become “intelligent” by connecting them with one another. On a construction site, the Internet of Things would allow construction machinery, equipment, materials, structures, and even formwork to “talk” to a central data platform to capture critical performance parameters. Sensors, near-field-communication (NFC) devices, and other technologies can help monitor the productivity and reliability of both staff and assets. There are several potential uses:
One popular form of NFC technology is radio-frequency identification (RFID). This is used extensively in logistics, retail, and manufacturing environments to collect precise information about a product, place, time, and transaction. Since the 1990s, construction has begun to use RFID for applications such as tracking materials and equipment and developing automated time sheets.
And NFC technology is evolving. Soon, tags will be able to include information on specifications, dates, defects, vendors and original equipment manufacturers, maintenance records, operating parameters, and other applications. Costs of RFID equipment, including scanners, receivers, and tags, are falling, and new applications are emerging. A British construction company, for example, is using RFID to monitor truck inspection, track tool usage, and train workers at construction sites. In addition to the opportunities from the Internet of Things, the greater use of digitization in the construction-planning process and on the construction site itself is enabling firms to capture data that paper could not. The insights gained through the adoption of advanced analytics in construction projects can help to improve efficiency, timelines, and risk management. Advanced analytics helped a major London infrastructure project save time and money when project leaders worked with a data analytics company to produce a web-based adaptive-instrumentation-and-monitoring system. The system absorbed field-sensor data, construction-progress data, and workforce and vehicle movements. Statistical analysis based on this information helped project teams detect anomalies and identify potential risks—critical information for a dense and historically sensitive city like London. Other examples abound. For instance, insights from advanced analytics helped an oil and gas giant improve the productivity of its engineering function by 20 to 25 percent by pairing the right teams, appointing appropriate team leads, and modifying their workflows to minimize waste and improve efficiency. In another case, a large Middle Eastern construction firm worked with a software company to build a predictive analytics engine to prevent equipment breakdowns on-site for its fleet of construction vehicles. This saved millions of dollars in downtime, fuel costs, and maintenance expenses. Event simulations, coupled with optimization algorithms, have also helped shipbuilders optimize construction planning.Other industries have shown that first movers can build a sustainable competitive advantage. In the construction sector, this is also likely to be the case. Over the next decade, these winners of tomorrow will take the lead in technology innovation and digitization. Resisting change is no longer an option.
Disclaimer: This is an excerpt from this article